The 'intelligent' robot companion that plays chess as a hobby, serves coffee and learns from its own experiences
Special Tradeshow Coverage for ATX West 2017
Meet the robot whisperer who trains "big, monstrous, industrial robots" to follow her every command
Dual Check Safety Improves Stop Position Prediction
Is a Robot After Your Job?
Foxconn reaches 40,000 robots of original 1 million robot automation goal
Japanese Robotics Giant Gives Its Arms Some Brains
Rethink Robotics Leads in Research and Education with Open Source SDK
Could the future of pizza be in the hands of robots?
Tag Team Manufacturing Speeds Delivery with Rethink Robotics' Sawyer
Kawasaki Robotics Releases the "duAro", a First-of-its-Kind Collaborative Robot, for North American Market
Global collaborative robots market expected to grow at a high rate
Ford's new robots can build cars, make coffee
Standardizing Collaborative Robots: What is ISO/TS 15066?
Rise in Robotics Requires New Tax Approach, EU Report Warns
Records 46 to 60 of 106
First | Previous | Next | Last
Featured Product
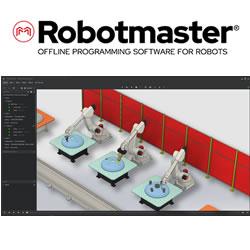