Automation for All
Why Are You Still Manually Programming Your Robot?
Working With Robots With Different Levels of Collaboration
Robotic Disruption in US Workforce Leads to New Opportunities and Challenges
Engineers Meet Industry Demand By Growing Their Robotics & IAS Expertise
ABB Robotics showcases future of retail using recovered marine plastic at London's Selfridges
Using an LVDT as a Robotic Micrometer or Automated Height Gauge
Making Robotic Programming Easier for the Fabrication Industry
ATX West and IME West 2022 Product Preview
Three Reasons to Robotize Soldering Operations
Learn How To Protect Your Business with AI for Visual Inspection - Pleora Webinar Live April 6, 2022
5 Robotics Trends in 2022
Robotic Resources: How Autonomous Technologies Enhance Human Capabilities
Automation for the Pharmaceutical Industry, Laboratories and Analysis.
How Computers Deliver the Ability to See
Records 376 to 390 of 2113
First | Previous | Next | Last
Industrial Robotics - Featured Product
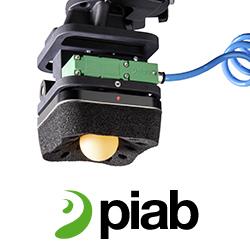