Ergonomic Under Load: Vacuum Handling Systems for the Logistics Industry
Seen, stored, learned - Self-learning robots solve tasks with the help of an Ensenso 3D camera
Cut From the Same Cloth - Automatic 3D Recognition and Marking of Wooden Beams
Good Things Come in Automated Packages
The Importance of a Reliable Supply Chain for Robotics Companies
The Incredible Potential of Soft Robotics
MODEX Q&A - Schmalz
MODEX Q&A - Honeywell Intelligrated
MODEX Q&A - PIAB
MODEX Q&A - Comau
Food Safety in Large Scale Picking of Produce
RoboticsTomorrow - Special Tradeshow Coverage MODEX 2020
Musashi AI Technology for Dynamic Environments
MARS - Mobile Arm Robot System
COMPUTER VISION AND ROBOTICS EXPAND INDUSTRIAL CAPABILITIES
Records 661 to 675 of 2113
First | Previous | Next | Last
Industrial Robotics - Featured Product
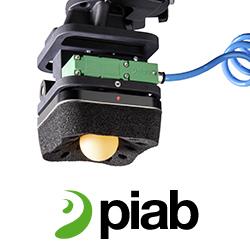