The Role of Smart Glasses as a Safe Return to Work Strategy
Business Perspectives and the Impacts of COVID-19 - Q&A with Honeywell Intelligrated
Today's Robotics Innovation Landscape and the Role of IP in The Field of Robotics
Business Perspectives and the Impacts of COVID-19 - Q&A with FAULHABER MICROMO
Business Perspectives and the Impacts of COVID-19 - Q&A with Parker LORD
Flexible Conveyor Manufacturer Glide-Line Overcomes Space, Size, & Product Handling Constraints for Aerospace Industry Integrator
Business Perspectives and the Impacts of COVID-19 - Q&A with BitFlow Inc.
Perceptions of Collaborative Robotics Post, COVID-19, Q&A with Productive Robotics
Surviving a Global Cyberattack - Company Culture Plays a Pivotal Role
The Importance of a Reliable Supply Chain for Robotics Companies
WCX World Congress
Robotic Assistance and the Future of Energy Sustainability
MODEX Q&A - Schmalz
MODEX Q&A - Mobile Industrial Robots (MiR)
MODEX Q&A - Honeywell Intelligrated
Records 106 to 120 of 171
First | Previous | Next | Last
Featured Product
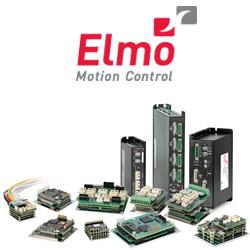